渗碳件常见缺陷与对策
1.降低表面碳浓度,扩散期内减少滴量和适当提高扩散期湿度,也可适当减少渗碳期滴量
5.提高淬火加热温度50~80ºC并适当延长保温时间
6.两次淬火或正火+淬火,也可正火+高温回火,然后淬火回火
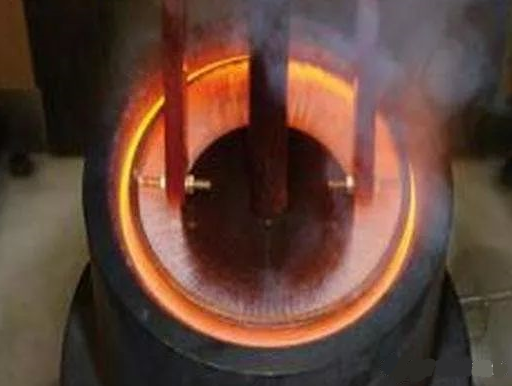
2.降低直接淬火或重新加热淬火温度,控制心部铁素体的级别≤3级
4.可以重新加热淬火,冷处理,也可高温回火后重新淬火
3.磨削余量,较大件允许有一定脱碳层(≤0.02mm)
缺陷产生原因:渗碳介质中含氧量较高:氧扩散到晶界形成Cr、Mn、Si的氧化物,使合金元素贫化,使淬透性降低
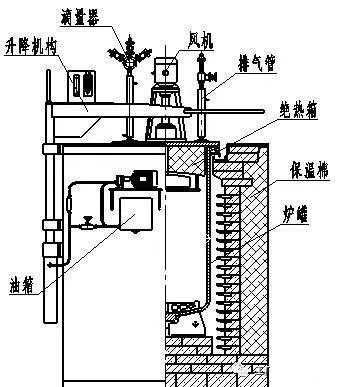
1.针对原因,调整渗碳温度、时间、滴量及炉子的密封性
4.渗层过薄,可以补渗,补渗的速度是正常渗碳的1/2,约为0.1mm/h左右
4.淬火温度高,溶入奥氏体碳量多,淬火后形成大量残余奥氏体
5.淬火加热温度低,溶入奥氏体的碳量不够,淬火马氏体含碳低
2.气体渗碳炉漏气固体渗碳时催渗剂在工件表面融化,液体渗碳后,工件表面粘有残盐
4.盐炉校正不彻底,空气炉无保护气氛加热,淬火后不及时清洗
缺陷产生原因:
1.冷却速度过慢,组织转变不均匀
2.合金钢渗后空冷,在表层托氏体下面保留一层未转变奥氏体在随后冷却或室温放置时, 转变成马氏体,比容加大,出现拉应力
3.第一次淬火时,冷却速度太快或工件形状复杂]
4.材质含提高淬透性的微量元素(Mo、B)太多等
对策:
1.渗后减慢冷却速度,使渗层在冷却过程中完全共析转变
2.渗后加快冷却速度,得到马氏体+残余奥氏体。松弛内层组织转变产生的拉应力
3.淬火开裂应减慢冷却速度、含微量元素作工艺试验,或提高淬火介质温度
3.渗后直接淬火,氢来不及析出以过饱和状态存在于钢中
3.零件出炉前停止供给渗剂,通入氮气排氢后,直接淬火
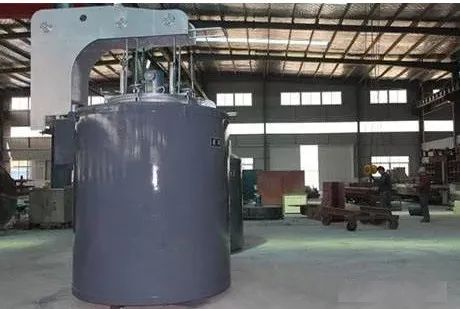
5.经常烧碳黑,清理炉内积炭,渗后入冷却井冷却,在井中倒煤油或甲醇保护
缺陷产生原因:
1.渗碳温度太高,保温时间太长
2.滴量过大,炉内碳势高
3.试样检验不准
对策:
1.针对原因,采取工艺措施
2.渗层超过图样上限要求,不合格,但与图样规定相差0.05mm时,可以仲裁合格或申请回用
7.零件上渗碳层的浓度和深度不均匀,淬火时造成无规则翘曲
8.工件形状复杂,壁厚不均匀,有的面渗碳,有的面不渗碳或少渗碳
1.长杆状件应垂直吊放,平板零件要平放,零件在夹具上要平稳不能受预应力,出炉操作要平稳、炉温要适当
2.直接淬火应预冷,尽量用一次淬火代替二次淬火,正确选择热处理工艺
缺陷产生原因:
1.温度过低
2.渗剂太多,零件表面积炭
3.渗剂含硫量过多
4.风扇轴承用MoS2润滑,润滑油进入炉内,使硫增加
5.风扇轴承漏气、氧气进入炉中
6.风扇轴冷却水渗漏入炉
对策
针对缺陷采取相应措施
2.渗碳温度过高,大量碳原子渗入工件表面来不及扩散,过渡不好形成表面碳浓度过高
1.将高碳势件在保护气氛中(碳势(体积分数)为0.8%)加热2~4h,以减少表面碳浓度
2.也可将此件在质量分数为3%~5%的苏打和木炭中加热至920~940ºC,保温2~4h,以减少表面碳浓度
1.固体渗碳时,渗碳中由于SiO2质量分数2%以上所致
2.SiO2高温和Na2CO3作用,生成玻璃状物质粘附在工件表面,形成凸瘤
渗碳件出现反常组织(游离铁素体,游离渗碳体或网状铁素体在二次渗碳体周围)
1.钢中和渗碳介质中含氧量过高所致,使淬火时出现软点使耐磨性降低
1.渗碳时过势或淬火加热时过势,使晶粒长大,脆性增加
2.渗碳时过势,不但表层含碳量增加,同时碳化物也增加,出现莱氏体